This website uses cookies so that we can provide you with the best user experience possible. Cookie information is stored in your browser and performs functions such as recognising you when you return to our website and helping our team to understand which sections of the website you find most interesting and useful.
Agronomics Portco: Onego Bio’s Pioneering Biotech Platform for Sustainable Egg Protein
April 9, 2024
It was autumn 2021, a rather cold and dreary day in Helsinki, (Helsinki is, following experience in the summer, very beautiful and bright), having just arrived from a flight. The Agronomics team were on a trip to Helsinki to meet Solar Foods, an existing portfolio company focused on producing protein from thin air. Naturally, we asked the CEO, Pasi Vainikka, if he knew of anyone else worth meeting ahead of this trip so that we could use our time well. He pointed us towards Maija Itkonen, to speak with who was seeking to build a company with the leading scientist from the esteemed VTT, the Technical Research Institute of Finland, Christopher Landowski. We were already well acquainted with the potential of leveraging recombinant engineering to transition beyond the production of enzymes, and insulin, to produce food ingredients such as egg proteins, including ovalbumin, via, what has now been coined precision fermentation (PF).¹
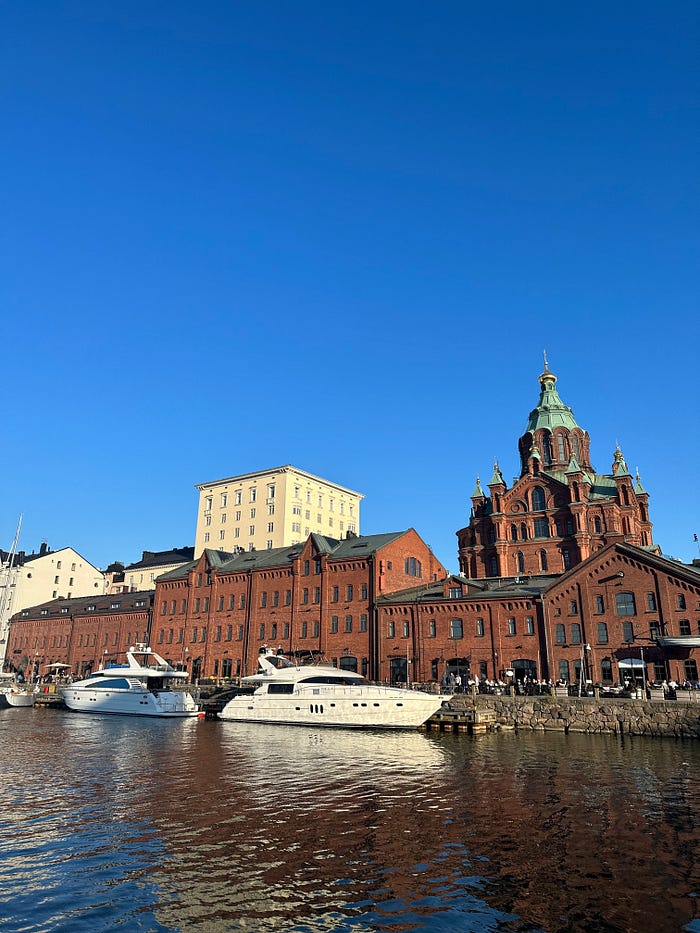
In early 2022, Onego Bio was formed and we led the €10 million seed round (formerly Project Eggplant), co-founded by Maija Itkonen, now CEO, and Chris Landowski, now CTO, with a €6.9 million investment from Agronomics. Maija is a seasoned entrepreneur and founder, described as “one of the most promising female entrepreneurs in Finland with her innovative thinking, drive and determination”. Her characteristics complement the depth and detailed technical knowledge of Chris, as co-founders together.
Two years later, an extreme acceleration of R&D at Onego Bio has culminated in an ample $40 million Series A led by Nordic Ninja, the largest Japanese-backed VC fund in Europe. Participation included from Finnish sovereign wealth fund Tesi and EIT Food, followed by follow-on participation from Maki VC, Holdix, and Agronomics. This influx of capital will not only drive the commercialisation and manufacturing of their animal-free egg protein, focusing on the United States but also pave the way for a more sustainable and efficient future of food production.
Egg: the king of protein
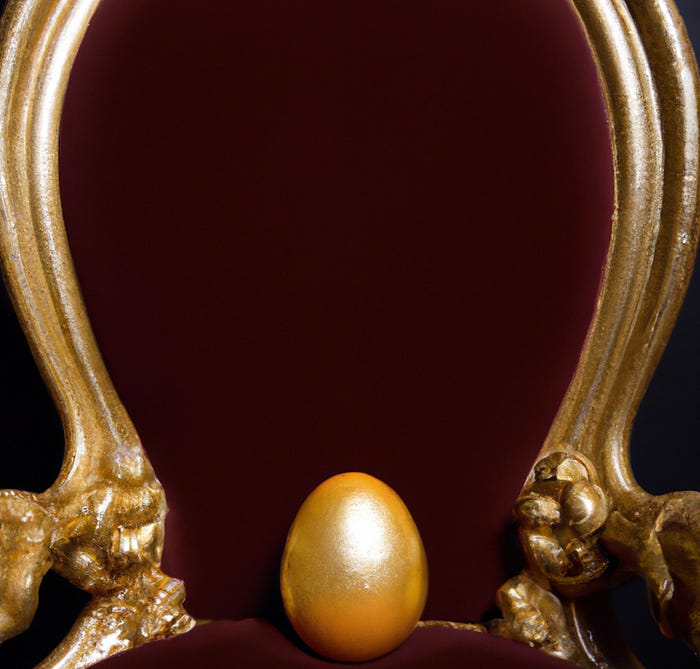
Eggs are a commendable protein source, serving as the benchmark for comparison for other protein sources, noting its PDCAAS (protein digestibility corrected amino acid score) score of 1.0, the protein quality assessor.² It is the egg white that contains the functionally important proteins — ovalbumin (54%), ovotransferrin (12%), ovomucoid (11%), ovomucin (3.5%), and lysozyme (3.5%).³ Each offers unique benefits — ovotransferrin is used as a metal transporter, antimicrobial, or anticancer agent, whereas lysozyme is mainly used as a food preservative. Ovalbumin is widely used as a nutrient supplement and ovomucin as a tumour suppression agent. Historically, separation methods derived from over a decade ago have been leveraged to isolate these individual proteins from the whole egg. Meanwhile, with PF, a modular approach can be taken to produce the targeted protein of interest. Egg whites, being ovalbumin, are vital functional binders for baked goods manufacturers, including familiar names — Mondelez, Grupo Bimbo, Flower Foods and Campbell Soup Company.. Onego Bio provides a bioidentical protein for conventional egg white, an easy switch for food formulators.
Trichoderma the Titan
(Note to reader: if the performance of microorganism strains doesn’t fascinate you like me, simply note that Trichoderma reesei is a powerful microorganism as a strain to produce recombinant proteins at very high titres — 100g/L+, necessary for viable unit economics, and skip this section)
Onego Bio has pioneered a transformative method for cost-effectively biomanufacturing ovalbumin, the most abundant protein found in egg whites, without chickens. Its proprietary Trichoderma reesei (T. reesei) fungal strains have the potential to achieve unrivalled protein titres exceeding 100g/L⁴, ⁵— multiples higher than competing common chassis such as yeast-based systems, Pichia pastoris (P. pastoris) and Saccharomyces cerevisiae, fungus, Aspergillus niger or the bacterium, E. coli. This is the critical gate to unlocking viable unit economics for producing food proteins, which are ultimately, commodities. There is a common debate with PF companies focusing on product vs. platform. I would emphasise the importance of having superior strain engineering tools and know-how around the chassis of choice, if opting for a product strategy, to ensure it is attainable from a cost perspective.
Generally speaking, the product-to-biomass ratio is higher with T. reesei than P. pastoris, indicating better conversion yields, meaning more of the substrate (glucose), is converted to product rather than cell biomass. Further, a higher product-to-biomass ratio with T. reesei over P. pastoris suggests a less intensive fermentation process, which has significant implications for fermentation scale-up, for instance, less oxygen demand, and less metabolic heat generated. Thus, with T. reesei, it is possible to manufacture at volumes above 250k L, if desired, whereas P. pastoris processes, with their high biomass demands, are less commonly found at larger scales.⁶
With P. Pastoris, It is common for methanol to be used as the carbon source for the expression induction step with a P. pastoris heterologous protein expression system.⁷ Methanol catabolism requires huge amounts of oxygen supply and a considerably exothermic process. Given this compound’s toxic and flammable nature, this offers safety handling concerns, especially at large-scale fermentation.⁸ I would note, that many P. pastoris protein expression systems have been modified to utilise a methanol-independent process, including the catabolic depression of glucose, utilising alternative promoters of P. pastoris (instead of the AOX1 promoter for recombinant proteins).⁹
The filamentous nature of the fungus T. reesei, meaning it is a saprophytic microorganism highly capable of secreting proteins, provides the advantage of lowering the cost base of the bioprocess, given that minimal downstream processing (DSP) steps are required to attain a protein with high purity. With a secreter system, simplistic centrifugation, or filtration can be utilised. Onego Bio has shown an impressive improvement in its downstream processing, with superior purities and recovery yields for ovalbumin. Noting the substantial capex cost DSP can burden on the bioprocess, the DSP for Onego Bio will continue to be optimised to improve yield further, as well as to align with contract manufacturing organisations (CMOs), see below, on the available DSP equipment.
Note both T. reesei and the team at Onego Bio have significant industry experience — a necessity for a biomanufacturing business. Arni Kujala, Head of Manufacturing at Onego Bio, was the former Head of Engineering at Roal Oy, one of the top five enzyme manufacturers in the world, who joined in 2023, and has been critical to implementing the scale-up strategy for their bioprocess.¹⁰ T. reesei has been used to produce industrial enzymes such as cellulases to break down cellulose for biofuels, textiles and in the food industry and pectinases to improve the quality of wines and textile manufacturing, so now, why not egg proteins?¹¹ (For instance, T reesei is used to produce the recombinant phytase as an additive for animal feed.)¹²
P. pastoris is unquestionably a versatile cell factory, proven at an industrial scale to produce valuable proteins such as insulin (since 1988 by Phillips Petroleum,¹³ which later partnered with Eli Lilly to produce the first recombinant human insulin protein FDA-approved, marketed as Humalog in 1996¹⁴), and the infamous GLP-1 agonists (glucagon-like peptide-1), and its analogues, to treat Type II diabetes.
A comparison — GLP-1s vs. ovalbumin (pharmaceutical vs food-grade)
Comparisons can be drawn with producing recombinant GLP-1 agonists vs. ovalbumin via PF. While Eli Lilly and Novo Nordisk market capitalisations (NYSE: LLY), (NVO.CO), are benefiting from the commercialisation of their GLP-1 agonists and the emergent trend of usage for the obese (and the not-so-obese) with their respective semaglutides — Ozempic and Wegovy. They have each spent billions on R&D for diabetes products. The pharmaceutical nature and protein complexity of the biologic GLP-1 drugs present a much higher risk profile toward commercialisation than the food-grade ingredient ovalbumin, and a much larger financial burden on the developer.
The beauty of PF food ingredients is the absence of clinical trials required for regulatory approvals. Ingredients derived from PF require FDA GRAS designation for commercial consumption in the US.¹⁵ Onego Bio expects to receive this in 2025 (three years after formation), coinciding with the first sales of ovalbumin to various clientele in the US. Whereas, the first clinical trials for semaglutides began in 2008, and Ozempic was approved by the US FDA nine years later, in 2017.¹⁶ (Ozempic Phase IIIa clinical trial programme did only take 18 months, but with 8,000 adult patients enrolled and eight individual clinical trials.¹⁷)
Both GLP-1 agonists and ovalbumin target enormous TAMs — GLP-1s target a 28 million US market of patients affected by Type II diabetes, whereas considering the commonly encountered ovalbumin, a survey by the American Bakers Association found that around 98% of Americans consumed baked goods regularly, with 60% consuming them daily — 180 million people.¹⁸ GLP-1 quantities of dosage are very small, at 5mg per person per week per dose, yet JP Morgan researchers views the production of GLP-1s as a $100bn biomanufacturing opportunity by 2030.¹⁹ Ovalbumin production presents an even larger opportunity.
This is why underwriting non-clinical biotech has the potential to be so powerful. With minimal regulatory and clinical risk, there is a huge potential upside from attaining a moat in an enormous global industry — if you select the right start-up, of course. This is the transition to biotechnology becoming ubiquitous and the expansion of the sustainable bioeconomy across numerous sectors, spanning food, industrials, energy, and materials.
Eggs are the new bitcoin
Onego Bio’s ovalbumin progress positions it as a frontrunner to become a major supplier of sustainable egg protein in the $270 billion global egg market, which is experiencing a 7.5% compound annual growth rate (CAGR) to a $387bn global egg market by 2028.²⁰ Extreme challenges exist in the existing market, with pricing variability due to a persistent fragile supply chain.

Egg prices have been scrambling skyward in recent years, with the fragility of the supply chain coming under scrutiny. Persistent outbreaks of avian influenza have decimated egg-laying flocks leading to egg shortages and pricing spikes. Just this month, Bloomberg reported on yet another outbreak of avian flu, with Cal-Maine Foods Inc., the largest egg producer in the US, culling 3.6% of its flock at a Texas facility.²¹ (Poor chicks) The USDA estimates that the 2022 influenza outbreak led to the deaths of over 58 million birds, making it the worst avian flu outbreak in US history. Eggflation spiked April 2023, however recent shocks have seen prices rise again.²²

The adoption of PF for food ingredients offers a powerful solution to rectify these pricing fluctuations and provide supply chain stability. Specifically for ovalbumin or other isolated egg proteins, the avoidance of utilising egg-layer flocks can additionally mitigate against pricing fluctuations in grain prices. Noting the increase in corn and soybean prices in 2022 as a consequence of Russia’s invasion of Ukraine, drought conditions and the fragility of a globalised supply chain.²³
Recent regulation has brought turmoil to US egg producers, who are rapidly shifting toward cage-free egg production. Ten states in the US, including California and Massachusetts, have implemented laws mandating the transition to cage-free housing systems for egg production by 2022.²⁴ ²⁵ Additionally, major food companies and retailers, such as McDonald’s USA, Walmart, and Costco, have announced their commitments to sourcing 100% cage-free eggs by 2025.²⁶ ²⁷ ²⁸
But does this not further incite a demand on supply causing eggflation? If major food manufacturers are all demanding the same cage-free eggs from the ten states they are available? Onego Bio and its PF egg proteins can help soothe and diversify supply.
Great America, the land of opportunity $$$

America, start-up nation and, now becoming the biomanufacturing leader, via the Democratic government, has launched several recent initiatives to bolster biotechnology and biomanufacturing in the country. On September 12, 2022, President Biden signed an Executive Order on “Advancing Biotechnology and Biomanufacturing Innovation for a Sustainable, Safe, and Secure American Bioeconomy.”, with $2bn of federal funding, leading to the Bold Goals for US Biotechnology and Biomanufacturing, a watershed moment for the industry.²⁹ Biotechnology growth in the US is foundational to the security of the economy and sustainability as supply chains move to be deglobalised. This is a huge sectorial tailwind for Onego Bio, and other biomanufacturing companies.
The White House further launched the National Biotechnology and Biomanufacturing Initiative (NBBI) to accelerate the growth of the US Bioeconomy. The Advanced Research Projects Agency for Health (ARPA), with a budget of $1 billion, focused on accelerating high-risk, high-reward research in biotech. The latest from the White House is the newly installed (last month) National Bioeconomy Board to complement the ongoing execution of the Bioeconomy executive order.³⁰
The USDA further supports biomanufacturing in the farm bill, the USDA Section 9003 program, also known as the Biorefinery, Renewable Chemical, and Biobased Product Manufacturing Assistance Program, offers $200 million and loan guarantees for biomanufacturing related to food.³¹ A powerful tool intended to promote rural development and job creation across the United States. Onego Bio is a candidate for this funding.
As the White House rightly says “Biotechnology harnesses the power of biology to create new services and products, which provides opportunities to grow the US economy and workforce and improve the qualities of our lives and the environment.” In short, manufacturing will become the same as biomanufacturing, the economy IS the bioeconomy.
VC investors also need to open their eyes and adjust to funding higher capex but higher return potential businesses that can build credible, solid IP moats, rather than investing in another software or GPT wrapper business.
“Partner with CMOs” Are there any CMOs???
(CMO = Contract manufacturing organisation)
An obvious risk factor that arises when diligencing biomanufacturing companies is the insufficient fermentation manufacturing capacity available on a commercial scale. Production scales above 50k litres are required to leverage economies of scale for an economically viable process. (Unless of course, considering continuous fermentation platforms such as POW.Bio or Cauldron — and I believe in a multi-pronged approach for unlocking more capacity). Synonym’s Capacitor.Bio states there is 50 million litres of active capacity worldwide, across 282 facilities and 43 countries.³² However, there are only a handful of CMOs with available capacity of more than 100k litres. As outlined in last year’s article — Biomanufacturing — the engine that will drive the future of food, site selection for CMOs is driven by minimising the cost structure — minimising costs of the carbon source, power and labour, making the midwest USA, a favourable location to break ground. (A perfect spot to have witnessed the eclipse also! — https://www.linkedin.com/feed/update/urn:li:activity:7183084540142215168/)
At Liberation Labs, industrial biotech’s fabrication partner, which Agronomics co-founded in 2022 to address this capacity bottleneck, we are bringing online a 600k litre food-grade fit-for-purpose fermentation plant by Q4’24, later this year. Building CMOs with food production in mind is a novel concept given most legacy sites are 40 years old. Onego Bio is well positioned to partner with existing CMOs and potentially partner with Liberation Labs in the future as we establish a network of multiple, 4 million litre fermentation plants across the globe. We need further investment in the infrastructure for biomanufacturing (and further innovation), whether from public or private sources.
Low COGs are key
The challenge with identifying CMOs is that while there may be capacity available, they are not at the right pricing needed to rent for certain bioprocesses to make them economically viable. Hence, it is important to focus on improving the strains — attaining the best titres and productivity possible so that more capacity is available at higher prices for the same COGs and or margins. It is much easier to attain an appropriate cost structure for glycoproteins such as lactoferrin for infant formula — $500/kg, than, say, whey protein <$5/kg. Ovalbumin cage-free market price is around $20–25/kg, battery-caged around $15–20/kg, which is attainable to deliver good margins.
The time for novel chassis // Avoiding sugar is the new oil
T. reesei is a powerful workhorse for the production of recombinant proteins for the reasons outlined above, and the strain engineering under Chris Landowski’s leadership at Onego Bio is unparalleled. However, the pursuit of novel chassis for other compounds and ingredients remains of great interest.
Less than 0.01% of nature’s biosynthetic diversity has been explored, and at least one trillion microorganisms in the world, there is reasonable evidence to suggest seeking novel chassis beyond the aforementioned.³³
All these microorganisms for PF metabolise carbon sources to generate cell biomass, and produce proteins. C6 sources, glucose, or its enantiomer dextrose, are favourite feedstocks for T. reesei (dextrose), and P. pastoris (glucose), as a result of their evolutionary adaptations. With the rise of the bioeconomy, glucose could become a popular resource — ‘sugar is the new oil’. To mitigate rising prices, we need commercial bioprocesses to utilise different carbon sources, or to avoid sugar from corn. This loops back to Solar Foods — their protein is a hydrogenotroph which feeds off hydrogen and CO2 from the air (not PF, but biomass fermentation). Cellulose is the most abundant sugar on the planet, and could be a viable feedstock.³⁴ Recent work by Cornell University, explored the engineering of Vibrio natriegens, to convert this microorganism from an obligate heterotroph (an organism that consumes organic compounds), to an autotrophic system (installing a non-native Calvin cycle to generate its own carbon source from CO2).³⁵ Simply, it is a zero-capital molecular biology route, removing the cost layer of the carbon source.
Anthology, with genome diversification technology from the George Church lab, is unlocking new possibilities for biomanufacturing. By accelerating the speed of genetic mutations and selection, microorganisms can be adapted to grow efficiently on renewable feedstocks, hence also aiding this trend towards a carbon-neutral or carbon-negative bioeconomy. They are leveraging machine learning to improve the target phenotype with alternative metabolic capabilities, titres and productivity. This is the digitisation of biomanufacturing — the marriage of AI and synthetic biology, a transformative trend for this decade.
With the present tailwinds, this coming decade could well be the time to put to bed whether the chicken or egg came first. Agronomics currently holds a 16.36% equity stake in Onego Bio on a fully diluted basis.
ENDS

- https://www.rethinkx.com/precision-fermentation#:~:text=Precision%20Fermentation%20(PF)%20is%20a,almost%20any%20complex%20organic%20molecule.
- Puglisi MJ, Fernandez ML. The Health Benefits of Egg Protein. Nutrients. 2022 Jul 15;14(14):2904. doi: 10.3390/nu14142904. PMID: 35889862; PMCID: PMC9316657.
- Abeyrathne ED, Lee HY, Ahn DU. Egg white proteins and their potential use in food processing or as nutraceutical and pharmaceutical agents — a review. Poult Sci. 2013 Dec;92(12):3292–9. doi: 10.3382/ps.2013–03391. PMID: 24235241.
- Landowski, C.P., Mustalahti, E., Wahl, R. et al. Enabling low cost biopharmaceuticals: high level interferon alpha-2b production in Trichoderma reesei . Microb Cell Fact 15, 104 (2016).
- Joel R Cherry, Ana L Fidantsef, Directed evolution of industrial enzymes: an update, Current Opinion in Biotechnology, Volume 14, Issue 4, 2003, Pages 438–443, ISSN 0958–1669,
- Pieter De Brabander, Evelien Uitterhaegen, Tom Delmulle, Karel De Winter, Wim Soetaert, Challenges and progress towards industrial recombinant protein production in yeasts: A review, Biotechnology Advances, Volume 64, 2023, 108121, ISSN 0734–9750,
- Karbalaei M, Rezaee SA, Farsiani H. Pichia pastoris: A highly successful expression system for optimal synthesis of heterologous proteins. J Cell Physiol. 2020 Sep;235(9):5867–5881. doi: 10.1002/jcp.29583. Epub 2020 Feb 14. PMID: 32057111; PMCID: PMC7228273.
- Wang J, Wang X, Shi L, Qi F, Zhang P, Zhang Y, Zhou X, Song Z, Cai M. Methanol-Independent Protein Expression by AOX1 Promoter with trans-Acting Elements Engineering and Glucose-Glycerol-Shift Induction in Pichia pastoris. Sci Rep. 2017 Feb 2;7:41850. doi: 10.1038/srep41850. PMID: 28150747; PMCID: PMC5288789.
- Wang J, Wang X, Shi L, Qi F, Zhang P, Zhang Y, Zhou X, Song Z, Cai M. Methanol-Independent Protein Expression by AOX1 Promoter with trans-Acting Elements Engineering and Glucose-Glycerol-Shift Induction in Pichia pastoris. Sci Rep. 2017 Feb 2;7:41850. doi: 10.1038/srep41850. PMID: 28150747; PMCID: PMC5288789.
- https://www.roal.fi/en/home/
- Kubicek C.P. (2013). Fungi and lignocellulosic biomass. John Wiley & Sons
- https://efsa.onlinelibrary.wiley.com/doi/full/10.2903/j.efsa.2022.7610#:~:text=The%20product%20containing%206%2Dphytase%20produced%20by%20a%20genetically%20modified,)%20and%20all%20pigs%20(piglets%2C
- Kjeldsen, T., 2000. Yeast secretory expression of insulin precursors. Applied Microbiology and Biotechnology, 54(3), pp.277–286.
- Gurramkonda, C., Zahnd, D., Lawry, J., Ranjan, A., Gafken, P.R., Marten, M., Ingram, J., Sarkar, C.A. and Tolbert, B.S., 2018. Purification of recombinant human insulin from Pichia pastoris. Protein Expression and Purification, 151, pp.25–33.
- https://www.fda.gov/food/food-ingredients-packaging/generally-recognized-safe-gras
- https://www.novonordisk.com/content/nncorp/global/en/news-and-media/news-and-ir-materials/news-details.html?id=667#:~:text=About%20Ozempic&text=The%20phase%203a%20programme%20involved,Canada%20on%209%20January%202018.
- https://www.clinicaltrialsarena.com/projects/ozempic-semaglutide-treatment-type-2-diabetes/?cf-view
- https://americanbakers.org/research-and-data
- https://www.jpmorgan.com/insights/global-research/current-events/obesity-drugs
- https://www.researchandmarkets.com/report/eggs
- https://www.bloomberg.com/news/articles/2024-04-02/top-us-egg-supplier-idles-texas-plant-after-bird-flu-outbreak?utm_content=business&utm_source=twitter&utm_medium=social&utm_campaign=socialflow-organic&cmpid=socialflow-twitter-business&embedded-checkout=true
- https://www.bloomberg.com/news/articles/2023-02-14/eggs-jump-8-5-as-worsening-us-food-inflation-socks-consumers
- https://www.ers.usda.gov/data-products/feed-grains-database/feed-grains-yearbook-tables/
- https://leginfo.legislature.ca.gov/faces/codes_displayText.xhtml?article=&chapter=13.8.&division=20.&lawCode=HSC&part=&title=
- https://malegislature.gov/Laws/SessionLaws/Acts/2016/Chapter333
- https://corporate.mcdonalds.com/corpmcd/our-stories/article/cage_free_farmer.html
- https://corporate.walmart.com/policies#animal-welfare-position
- https://customerservice.costco.com/app/answers/answer_view/a_id/1197/~/what-is-costco%E2%80%99s-statement-on-eggs%3F
- https://www.whitehouse.gov/briefing-room/presidential-actions/2022/09/12/executive-order-on-advancing-biotechnology-and-biomanufacturing-innovation-for-a-sustainable-safe-and-secure-american-bioeconomy/
- https://www.whitehouse.gov/ostp/news-updates/2024/03/22/the-white-house-advances-biotechnology-and-biomanufacturing-leadership-with-the-launch-of-the-national-bioeconomy-board/
- https://www.rd.usda.gov/programs-services/energy-programs/biorefinery-renewable-chemical-and-biobased-product-manufacturing-assistance-program
- https://capacitor.bio/
- Locey, K. J., & Lennon, J. T. (2016). Scaling laws predict global microbial diversity. Proceedings of the National Academy of Sciences, 113(21), 5970–5975. https://doi.org/10.1073/pnas.1521291113
- https://forest.fi/article/st1-aims-to-increase-its-production-of-wood-based-bioethanol-15-fold-by-products-of-forest-industry-replace-fossil-raw-materials-and-increase-carbon-sink-in-agricultural-lands/#7eb5b738
- David A Specht, Timothy J Sheppard, Finn Kennedy, Sijin Li, Greeshma Gadikota, Buz Barstow, Efficient natural plasmid transformation of Vibrio natriegens enables zero-capital molecular biology, PNAS Nexus, Volume 3, Issue 2, February 2024, pgad444